Pre Engineered Steel building system is a combination of built up sections (fabricated from steel plates), hot rolled sections and cold formed sections with different type of roof and wall claddings. This provides a complete building system which is airtight, energy efficient, optimum in weight and cost with speedy construction. Built-up and Hot rolled sections are called Primary steel members whereas cold formed sections are called secondary steel members.
These buildings are made water tight by use of bead mastic, filler strips & trims and flashings. Further flexible which can be finished internally to serve any required function and fit out externally to achieve attractive architectural elegances. Ideal for Warehouses, Manufacturing facilities, Super markets, Storied Car parks, Fuel stations, Offices, Houses, Commercial showrooms, Shops, Stadium, Aircraft Hangers,& Mixed developments.
Presently Light gauge steel (LGS) are used for Temporary buildings, Labour camps, Portacabins (site office facilities) including residence buildings up to G+2. Members are designed and roll formed by “Frame Cad” Machine.
The primary members (portal/mainframes) basically tapered column& tapered rafters (built up sections from steel plates) fabricated by welding two flanges and a web. Splice plates are welded at the ends which are bolted when erecting the buildings.
Secondary members Purlins, Girts and Eave strut are cold formed manufactured by bending from steel coil of various thickness as per the design, to required shape “Z “or “C”. Normally 1.5mm to 3mm depending on the span and the design loads. Purlins are supporting the roof panel, Z Purlin are used commonly to increase the stiffness whereas Girts are used to provide frame work for wall cladding.
|
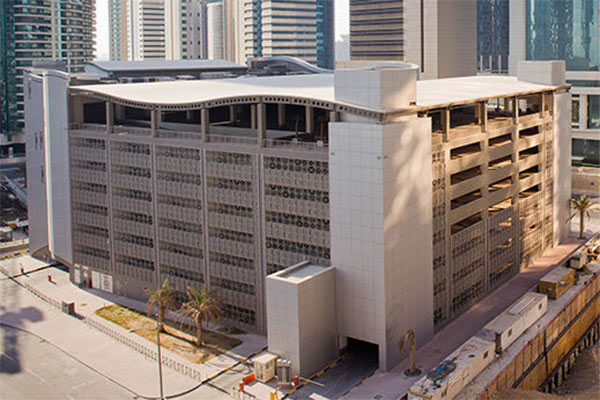 |
|
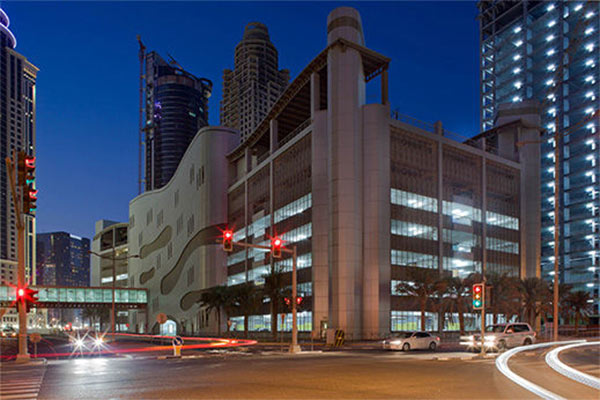 |
|
CONSTRUCTION OF MULTI-STOREY CAR PARK (G+6+P) FOR THE MINISTRY OF URBAN PLANNING AND DEVELOPMENT AUTHORITY, DOHA , QATAR.
8-level car park - 1,000 nos. capacity Duration: 24 Months, Total Built-up Area - 50,000 sqm
|
|
Surface preparation and pain system
Surface preparation for primary steel member are done as per the Swedish standard SA-2 to SA-2.5 by sand blast or shot- blast before applying red-oxide or Epoxy primer of about 75 microns , mid coat and top coat as per project requirements. Another option is to go for hot-dip galvanize for better protection.
Some projects steel structures are fire proofed by intumecent paint or cementitious paint for different DFT (dry film thickness) for 1 hour or 2 hour fire proof requirements as required.
Secondary members are normally pre-galvanized steel of 275g/m2
Roof & Wall cladding Panels
Early period Single skin profile sheets are used with insulation (foil faced Rock wool/Glass wool) for wall & roof cladding, which is economical. Double skin sandwich panel with PU (polyurethane) ,PIR (Polyisocyanurate) and MWF ( Mineral wool) insulation are used to achieve specified u value inside the building especially temperature controlled warehouses and cold storage. Better U value can be easily achieved by standing seam roofing system.
Base material of panels are generally Mild steel, Aluminium and Stainless steel with galvanized or Zincalum ( Zn 45% and Aluminium 55%) coating with required top color coat as per the requirements, special paint like PVDF ( Polyvinylidene difluoride) also available in the market to withstand various kinds of environmental hazards which excellent weathering resistance, acid/alkali resistance and self-cleaning performances. Below given are some tentative U value (Thermal transmittance) for different type of roofing and wall cladding systems.
Single skin with 50mm insulation approximate U value = 0.80 Wm2/K
Sandwich panel with 50 PIR or PU insulation approximate U value = 0.42 Wm2/K
Standing Seam roofing of 120mm insulation approximate U value = 0.30 Wm2/K
|
|
|
|
|
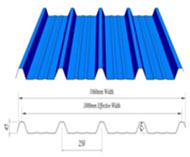 |
|
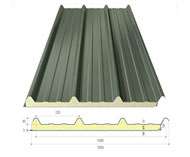 |
|
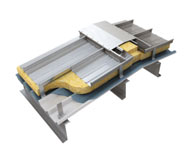 |
Single Skin |
|
Sandwich panel (Inner & Outer skin) |
|
Standing Seam (Liner & Outer skin) |
|
|
|
|
|
Panel thickness starts from 0.4mm up to 1.2 mm which is used as per the project specification and exposure conditions such as marine, chemical and industrial exposures to prevent corrosion and deterioration.
Panel can be manufacture to any length but usually 12m due to transportation, but roll forming can be carried out at site with no limit of length, Joint less roof (without end lap)and minimum pitch which is normally 1:20 (3deg). In standing seam roofing system the pitch can go up to 1:50 (1 deg).
At Erection columns are erected first and then the rafters are assembled, bolted and lifted by using cranes. Temporary trifor-winch, stay wires are used until complete the frame work as required with the bracings up to braced bay. Generally the designer provides few braced bay as required, also it is not advisable to continue the erection at, above20km/hour windy conditions.
Maintenance of steel building is less compared to conventional building. Once the roof work completed the whole roof need to be sweep for any drilled particles, debris screws left-over’s etc. , then once in a year inspection and cleaning is required to remove the accumulated dust and to clean the Gutters from dust, leaves from trees and growing plants.
Design code used in PEB: British codes BS-5950 and American Design codes AISC-2016 and material as per ASTM/JR, Structural welding as per AWS D1.1, MBMA -2012, AISI-2013 cold formed code and IBC-2015 Building code.
Design loads considered: Live load, Dead load, Collateral load, Wind load, Seismic load, Thermal load, Sand Load and rain fall intensity.
Finally in my opinion PEB concept and LGS concept is very good system for Sri Lanka specially to reduce the Housing problem and parking issues in cities, which can be done very fast in design and construction and no curing required, compared to conventional construction. Also can be achieved LEED green building certificate without difficulty since the material has sufficient recycle contend and the building would be energy efficient.
References:
- Technical Manual Pre-Engineered Building - Zamil Steel
- Insulated Roofing System Manual - Kingspan
- Pre - Engineered Metal Buildings - Lloyd Insulations (India) Limited
|